 
- UID
- 863084
|

本文介绍了锂电池自动贴胶机的工作原理,设计并实现了以CP1H系列PLC为基础的锂电池自动贴胶机控制系统,重点介绍了控制系统的工作原理、硬件配置、软件设计和故障排除及其维护。该系统已通过实际生产的应用得以验证,积累了宝贵的经验,在教学方面具有较好的应用价值。
1.引言
随着国家对新能源汽车产业扶持的力度逐年加大,其核心能源领域-动力锂电池将进入行业发展的高速期。相对于传统能源电池,锂电池具有能量密度高、重量轻、使用寿命长、绿色环保、重复利用率高等特点。目前,制造锂电池主要采用两种制造工艺,一种是卷绕,另一种是叠片,而制造大容量的新能源锂电池往往采用叠片工艺。叠片锂电池的核心部件-电芯的最后一道工序就是贴胶。随着客户对产品的工艺水平、效率和质量的要求越来越高,传统的手动贴胶已经不能满足现代生产的要求,所以研究高效、自动的贴胶机是市场的迫切要求。本文着重介绍了一种基于PLC的锂电池自动贴胶机控制系统,并且对系统的硬件和软件设计进行了详细的阐述。
2.锂电池自动贴胶机的工作原理
锂电池自动贴胶机是具有自动取料、贴胶、短路检测和下料功能的全自动包装设备。
其工作原理是在自动叠片机生产锂电池电芯的同时,进行自动备胶带工作。该工序涉及到的具体步骤是压胶、夹胶、拉胶、切胶和真空吸附五个过程。待叠片机生产出锂电池电芯之后,取电芯机械手把叠片台上的电芯取出,并且通过丝杆传送到贴胶机下进行贴胶。由于叠片工艺生产的电池体积比较大,贴一道胶带往往达不到紧固电芯的目的,所以这里设计了贴三道胶工序。每贴一道胶之后,电芯移动一段距离(该距离可以通过触摸屏设置),同时自动贴胶机进行备胶带工作,等备胶带工作完毕和取电芯机械手停止之后,进行贴胶工序,这样反复三次。每贴一次胶,通过光电颜色传感器检测胶带是否贴上,如果贴胶带正常,则进行下一道工序,如果贴胶带不正常,则返回上一个贴胶位重新贴胶。贴胶带工序完成之后,取电芯机械手运送贴好胶带的电芯到短路测试位,用短路测试仪进行短路测试,如果合格则运送到下料传送带下料,如果不合格则运送到废料箱下料。
3.电气系统的硬件设计
3.1 PLC选型
在自动贴胶机电控部分设计中,考虑到贴胶机的工序多,运行复杂,而PLC具有可靠性高、控制功能强、编程方便、易操作等优点,因此本文作者采用可编程逻辑控制器作为其核心控制部件。该控制系统采用日本欧姆龙公司生产的SYSMAC CP1H-XA40DT-D型号的PLC,该PLC的CPU单元本体采用DC24V电源,DC24V输入,晶体管漏极输出,内置输入24点、输出16点,并且可实现高速计数器4轴、脉冲输出4轴。基本指令每步0.1微秒,程序容量最大20K步,指令种类约400种,是一种功能强大的小型整体式PLC.由于其结构紧凑,功能强大以及性价比较高等特点,非常适合本系统的设计要求。
3.2硬件配置
系统的硬件配置结构框图如图1所示,包括CPU单元、输入(光电位置开关和贴胶有无检测传感器)、操作面板(触摸屏和指示灯)、控制元件(伺服驱动器和电磁阀)、执行部件(伺服电机、直流电机、气缸)等几部分组成。取电芯电机设置左限位、右限位和原点;拉胶气缸、切胶气缸和贴胶气缸各有两个光电位置开关用来检测气缸是否到位;贴胶有无检测传感器检测每次贴胶的胶带是否贴在电芯上。触摸屏作为设备控制的操作界面,接受来自操作人员的操作指令并指示设备的运行状态,PLC和触摸屏之间通过RS232通信电缆进行通信。取电芯电机采用伺服电机,通过伺服驱动器控制;下料电机采用直流电机;电磁阀采用两位五通的电磁阀来控制气缸的进退。
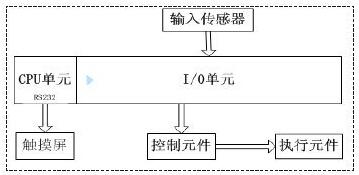
图1 系统硬件配置结构框图
3.3输入输出点的分配
自动贴胶机的生产过程是由取料、贴胶、短路检测、下料等几部分组成的。自动贴胶机的PLC输入信号包括:启动、停止(做完一个循环停止)、急停、取电芯电机前限、取电芯电机原点、取电芯电机后限、取电芯电机报警、贴胶好坏检测、短路检测、拉胶气缸出限、拉胶气缸回限、切胶气缸出限、切胶气缸回限、贴胶气缸出限、贴胶气缸回限。输出信号包括:取电芯电机正转、取电芯电机反转、下料电机正转、下料电机反转、取电芯气缸电磁阀、压胶带气缸电磁阀、夹胶带气缸电磁阀、拉胶带气缸电磁阀、切胶带气缸电磁阀、胶带真空电磁阀、贴胶带真空电磁阀、短路检测气缸电磁阀。
4.控制系统的软件设计
自动贴胶机控制系统的程序由两部分组成:一是触摸屏程序,二是PLC程序。
4.1触摸屏程序
触摸屏程序完成操作人员同PLC之间的对话,主要由自动操作、参数设定和手动操作三部分组成。其中自动操作主要由启动、停止和急停三个按钮组成,分别用来控制机器的启动、停止(做一个循环后停止)和出现紧急状况后停止用;参数设定主要用来输入第一道、第二道和第三道胶带相对于取电芯电机原点的位置;手动操作主要由气缸手动和电机手动两部分组成:气缸手动按钮用来手动控制系统中各个气缸的进退,电机手动按钮用来手动控制电机的正反转。本控制系统的触摸屏采用步科公司生产的Eview MT510.
4.2 PLC程序
自动贴胶机的主程序流程图如图2所示,首先进行初始化操作,取料电机回到原点,所有气缸回到初始状态。然后判断电芯是否叠好,如果没有叠好则继续等待,如果叠好了,取电芯机械手取电芯到第一道贴胶位进行贴胶,贴胶完毕后(贴胶气缸回到初限位),取料机械手取电芯到第二道贴胶位进行贴胶,以此类推到第三道贴胶位贴胶完成。在此过程中每贴一道胶带之后颜色传感器进行贴胶有无检测,如果没有检测到胶带则重新贴胶。贴完三道胶带之后进行电芯的短路检测,如果电芯的正负极短路,则把电芯放入废料盒,如果正负极绝缘性良好,则把电芯放到传送带上,同时启动传送带电机把电芯传送到下一道工序。到此为止一个循环完毕,开始下个循环,直到按下停止按钮为止。
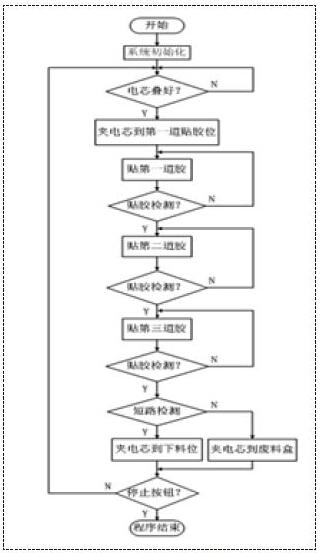
图2 系统硬件配置结构框图
5.结语
本方案中所设计的自动贴胶机是根据客户反映的叠片机生产出的电芯下料难、人工贴胶效率低以及没有短路检测功能而设计的。主要用于对前期叠片机的更新改造。根据客户反馈的情况,达到了客户的要求和预期设计效果,效率有了很大的提高,而且减少了人力,提高了自动化水平,使锂电池电芯加工工序全部实现自动化,从而证实了本方案的实用性。 |
|