在可预见的将来,功率电子元件的使用将持续不断的增加。任何需要电力变换、转换或控制等功能都须使用各种形式的功率电子元件。现今功率电子元件已广泛应用于各种不同的行业(图1)。灰色圆圈所代表的是需要使用功率模组的行业,如汽车业(电动车、混合动力车、燃料电池车等其他轮式车)、可再生能源业(太阳能逆变器、风力发电机、太阳能电站、卫星太阳能面板)、铁路设施(引擎元件、牵引控制系统)及高阶马达驱动器。这些功率电子元件一般由多种绝缘闸双极性电晶体(IGBT)或金属氧化物半导体场效电晶体(MOSFET)组成。

图1 功率电子元件的应用。灰色圆圈表示须使用大功率模组的行业。在大功率电子行业中,电动汽车、混合动力汽车及其充电站对功率电子元件的需求都有显著增长。
功率元件可靠性挑战倍增
对于使用IGBT或功率MOSFET的用户而言,可靠性是他们关注的首要议题。在这些行业中,产品的高可靠性和长使用寿命尤其重要。用户期望电动车在连续 15?20年内不出现任何重大维修问题;而铁路产业则须持续使用至少30年或更久。对于时常派遣维修人员对离岸风力发电机进行维修显然是不可行的,卫星太阳能面板甚至须永久性的使用。
热失效是高可靠性无法实现的主因。功率循环会使IGBT晶片端产生的热通过模组,并散发到周围环境中,其产生的应力及热会破坏模组。焊线可能因疲劳老化的原因而脱落或断裂,甚至进一步恶化导致完全失效(图2)。模组的堆叠层,特别是晶片焊接处,会因热-结构应力的作用下而脱层并破裂。在完全失效前,这些模组本可承受上万、甚至数以百万的功率循环次数。
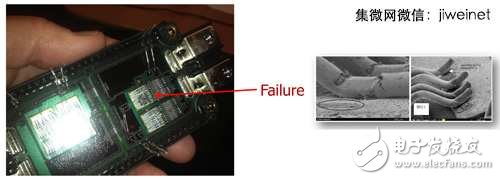
图2 IGBT模组产生故障的原因有很多种,包括焊线老化或脱落。 那么,我们如何保证这些模组在其应用领域中能持续使用多年,并耐受成千上万次功率循环呢?这不仅仅是功率电子模组供应商的责任,亦是相关产业供应商皆须克服的难题,无论是初期零组件供应商,抑或是原始设备制造商(OEM)均责无旁贷。若所生产的功率模组太早出现损坏的情况,则OEM应该为此负担保固、产品召回、声誉受损等损失。
功率模组的可靠性测试并不是一项新的挑战,但传统的模组测试过程非常漫长且具有不准确性和不确定性(图3)。一般可靠性的测试会将IGBT模组安装于设备上,并提供规定的安培数进行功率循环的测试。元件在经过多次功率循环测试(500次、1,000次、5,000 次等)之后,用户须将模组从设备上取下送往实验室进行检验,确认是否有无故障。若没有故障则继续重复该循环测试直至模组最终失效为止。此时模组将被再次送往实验室进行检查,藉由X光、声测、目测或破坏性的解剖方式来确定故障的原因。
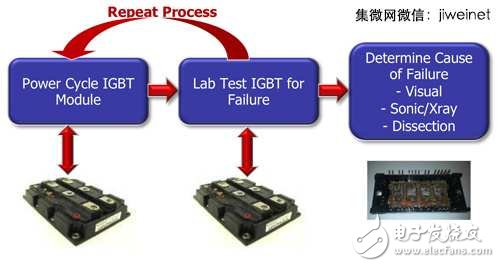
图3 传统的IGBT模组可靠性测试方法耗时、准确性低,无法在测试过程中即时观察到失效的产生,只能确定最后产品是否失效。
重复的功率循环测试和实验室检验非常耗时且无法在测试过程中即时观察到失效的产生,只能在最后确定元件是否失效。而若因多种不同原因所引起的失效,则可能无法确定其确切的原因。
新的可靠性测试方法应运而生
我们需要一种更有效、快速确定失效原因的测试方式。此方法要能在功率循环测试时量测模组中的电/热效应,并即时发现失效原因而不是依赖事后的诊断。为了满足以上的需求,唯有将功率循环和量测整合于同一设备中才能实现,使用户毋须将模组从功率循环测试设备上取出送往实验室进行失效分析。明导(Mentor Graphics)新推出的MicReD Industrial Power Tester 1500A就能提供这样的测试环境。
图4是功率测试设备进行功率循环和即时量测/诊断的示意图。该测试设备利用MicRed T3Ster暂态热特性技术对元件进行量测(如晶片封装、LED和系统)。主要特征有:
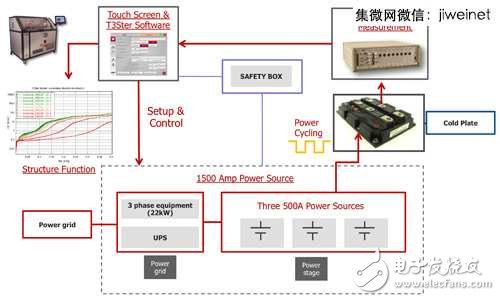
图4 测试设备整合功率循环和即时量测的方法,可即时监控模组的失效并减少实验室的事后分析。 .采用触控萤幕来控制、定义模组的特性和测试顺序及方法
无论是专家、产品工程师或技术人员都能简单的学习和使用。软体能储存相关的参数供重复使用,能用来测试多个产线上的样本或产品品质可靠性。
.1500安培的电源可同时提供三个不同的模组进行测试,每个模组可单独使用的电流高达500安培。
电源切换的时间仅需不到100微秒,这也是T3Ster设备在高准确性暂态热特性测试中所要求的速度。
.循环测试时,用户可自行定义时间间隔来量测、纪录模组的顺向电压变化,其最大取样速率高达每秒一百万个样本。
这些资料都将显示在触控萤幕上,并直接产生出结构函数。
.藉由结构函数可即时分析模组各层结构,并发现任何因失效所可能产生的变化(晶片或黏接层脱离、破裂等)。
这些资讯都能协助确定失效产生的确切时间和原因。
.安全盒会监测任何潜在的危险因素,如烟、冷却板液体泄漏、设备过热等。
一旦侦测到这些因素,测试设备将马上关闭所有的电源;但为保存测试资料,不断电供应系统(UPS)仍将继续为电脑供电,直至所有资料得到安全保存。结构函数精密分析重要性大增
结构函数的数学运算相当复杂,但值得花时间了解这相关的技术。图5是一个典型的模组堆叠层及其对应的结构函数示意图。在功率循环测试时,高功率(最大 1,500安培)会输入至元件来进行加热,待稳态后则迅速关闭。依照JESD51-14标准,精细的(微伏)接点正向电压变化会被量测纪录下来,同时藉由复杂的数学演算来建立出结构函数。

图5 典型的模组堆叠层及其对应的结构函数 功率电晶体接点所产生热会经过各堆叠层,最终扩散到周围环境中,而结构函数显示出元件堆叠层的等效模型,同时亦表示热传导路径上的热阻和热容特性。沿着图中的黑色曲线可了解接点到周围环境中的整体热传路径,横轴部分代表堆叠层的热阻(如晶片焊点、基板焊点及导热膏),其结构较薄,无法储存太多热量,但热阻较大。相反地,曲线中相对垂直的部分,则代表有较大热容的堆叠层(储热能力较高,同时也会产生一些热阻),如基板。
结构函数会记录元件在功率循环测试过程中的即时变化,当发现结构函数出现变化时,如图6中所出现的较长的热阻部分,这表示堆叠层中某一层(这里指的是基板焊锡层)发生变化。典型的热阻显著增加可能是因为堆叠层脱层或破裂的关系,因为空气的热传导能力明显低于变化前固体的热传导能力。
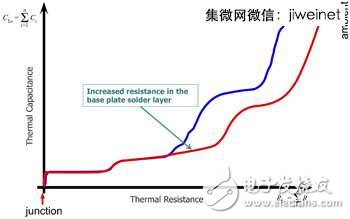
图6 某层(灰线标注)热阻的增加可能预示着该层脱层或破裂。 图 7是个实际的例子。该测试中,每五千次的功率循环测试都会撷取一次结构函数。从测试开始到第一万五千次功率循环测试后,线1所呈现的线形基本上不变,表明元件无任何失效或故障。在第二万次功率循环测试后(线6),我们看到曲线有细微的偏差,这说明某层结构的热阻开始升高。在之后的二万五千、三万和三万五千次功率循环后,线型显示某层结构出现显著劣化,最后导致元件失效。藉由结合功率循环与即时监控结构函数的方式,可以观察到失效的产生并确定失效的原因,毋须将元件从测试设备上取出,即能对测试结果进行分析诊断。
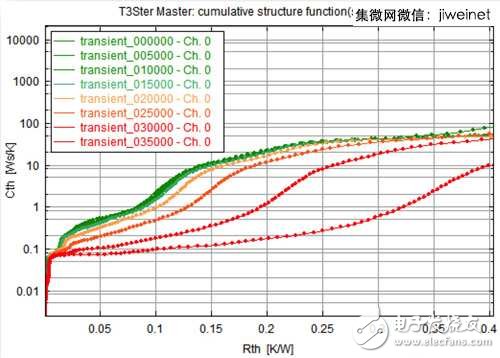
图7 元件在功率循环测试三万五千次后明显失效 与传统测试方法相比,此测试系统具有明显的优势。传统方法须要反覆循环测试、拆卸元件、实验室验证等过程,非常耗时且无法确定故障原因。采用结合系统和结构函数的技术,用户可设置测试顺序,并自动执行指令,将一开始正常的元件进行测试,直至产品失效,并能即时观察元件失效或故障的原因。此外,此设备可提供较大的电流,供应多个元件同时测试,从而提高处理能力,满足产品样本或品质测试的需求。
摆脱传统测试方式弊病 结合功率循环/量测系统势起
此测试设备可广泛应用于供应链中的各厂商,如功率电子模组供应商在模组的设计阶段可使用该测试设备。设计完成后的样本生产过程中,同样可使用功率测试设备来测试样本的可靠性指标;若无法通过测试,则可对产品设计进行修改。此外,测试设备还能用来产生产品资料表上的可靠度规格,在生产过程的产品抽验也能使用此设备。
初期元件供应商可使用功率测试设备,以验证功率电子供应商所提供的可靠度规格,对原始设计进行测试。最后,高可靠度产品的制造商可藉此设备,以进行最终的合格性测试,保证公司产品的高品质。 |